Introduction
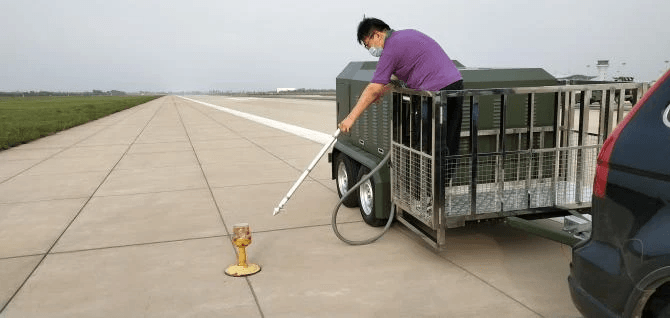
Testing high-friction materials is crucial to airport runway safety. An aircraft's ability to brake effectively and maintain control during landing or takeoff depends on the friction between its tires and the runway surface. Factors such as weather conditions, surface contaminants, and material composition can significantly affect runway friction, making investing in advanced friction testing technology essential.
Importance of Testing High-Friction Materials on Airport Runways
Using high-friction materials on airport runways is vital in ensuring safe and efficient aircraft operations. These materials are designed to provide superior traction and reduce skidding, enhancing overall runway safety. To maintain the effectiveness of these surfaces, regular testing using specialized equipment such as the airport surface friction tester is necessary.
Factors Affecting Runway Friction
Several factors can impact the friction levels on airport runways, including weather conditions like rain, snow, or ice. Surface contaminants such as rubber deposits from aircraft tires can also reduce friction over time. Understanding how these variables affect runway performance is important for implementing effective maintenance strategies.
Advancements in Friction Testing Technology
With technological advancements, friction testing apparatuses have become more sophisticated and accurate. Friction sensors can now measure and analyze surface friction with precision, providing valuable data for maintaining safe runway conditions. The development of high-friction surfacing has also contributed to improved traction and braking performance for aircraft.
Understanding High-Friction Materials
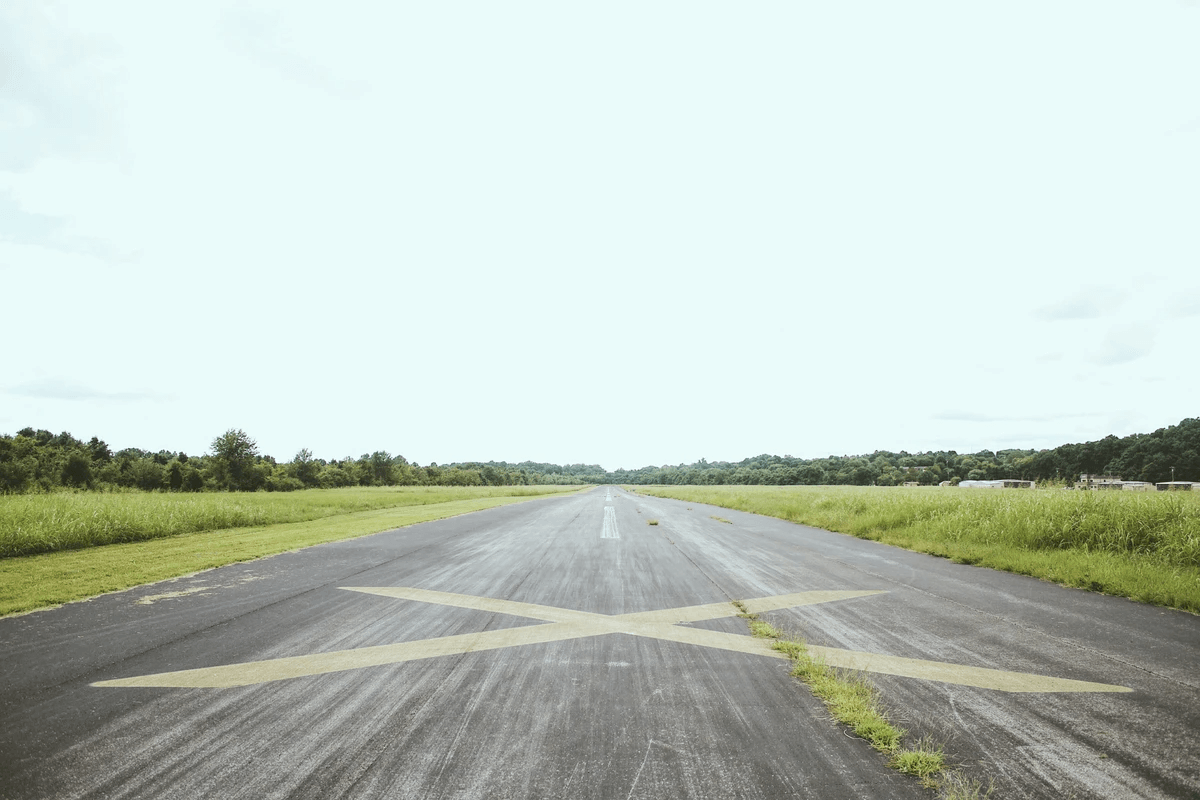
Definition and Characteristics of High-Friction Surfaces
High-friction surfaces are materials designed to increase traction and grip, particularly in areas with heavy traffic, such as airport runways. Traction and grip, particularly in areas with heavy traffic, such as airport runways. These surfaces are engineered to withstand the impact of aircraft landings and takeoffs, offering superior skid resistance and reducing the risk of accidents.
High friction surfaces are essential for airport runways as they provide the necessary traction and grip required for safe aircraft operations. These surfaces are specifically engineered to endure the immense impact of aircraft landings and takeoffs, ensuring that pilots can maintain control during critical moments. By offering superior skid resistance, high-friction surfacing significantly reduces the risk of accidents, providing peace of mind for both air traffic controllers and passengers alike.
Benefits of High-Friction Surfacing for Airport Runways
High-friction surfacing on airport runways offers significant advantages. Primarily, it enhances safety and operational efficiency.
Specifically, these materials:
- Improve braking efficiency, reducing stopping distances.
- Enhance safety during adverse weather conditions, such as rain and snow.
- Reduce runway maintenance costs by minimizing wear and tear.
- Extend the lifespan of runways through decreased deterioration.
Furthermore, high-friction surfacing helps prevent hydroplaning, a critical safety factor that can cause loss of control during takeoff or landing. By providing superior traction, these materials contribute to smoother and safer airport operations.
Implementing high-friction surfacing on airport runways is essential for ensuring the safety and efficiency of air travel.
Types of High-Friction Materials Used in Runway Construction
Various high-friction materials, such as epoxy-based aggregates, synthetic resin binders, and specially graded-calcined bauxite aggregates, are utilized in runway construction. These materials are carefully selected based on their durability, resistance to environmental factors, and ability to maintain consistent friction levels over time.
Friction Testing Apparatus
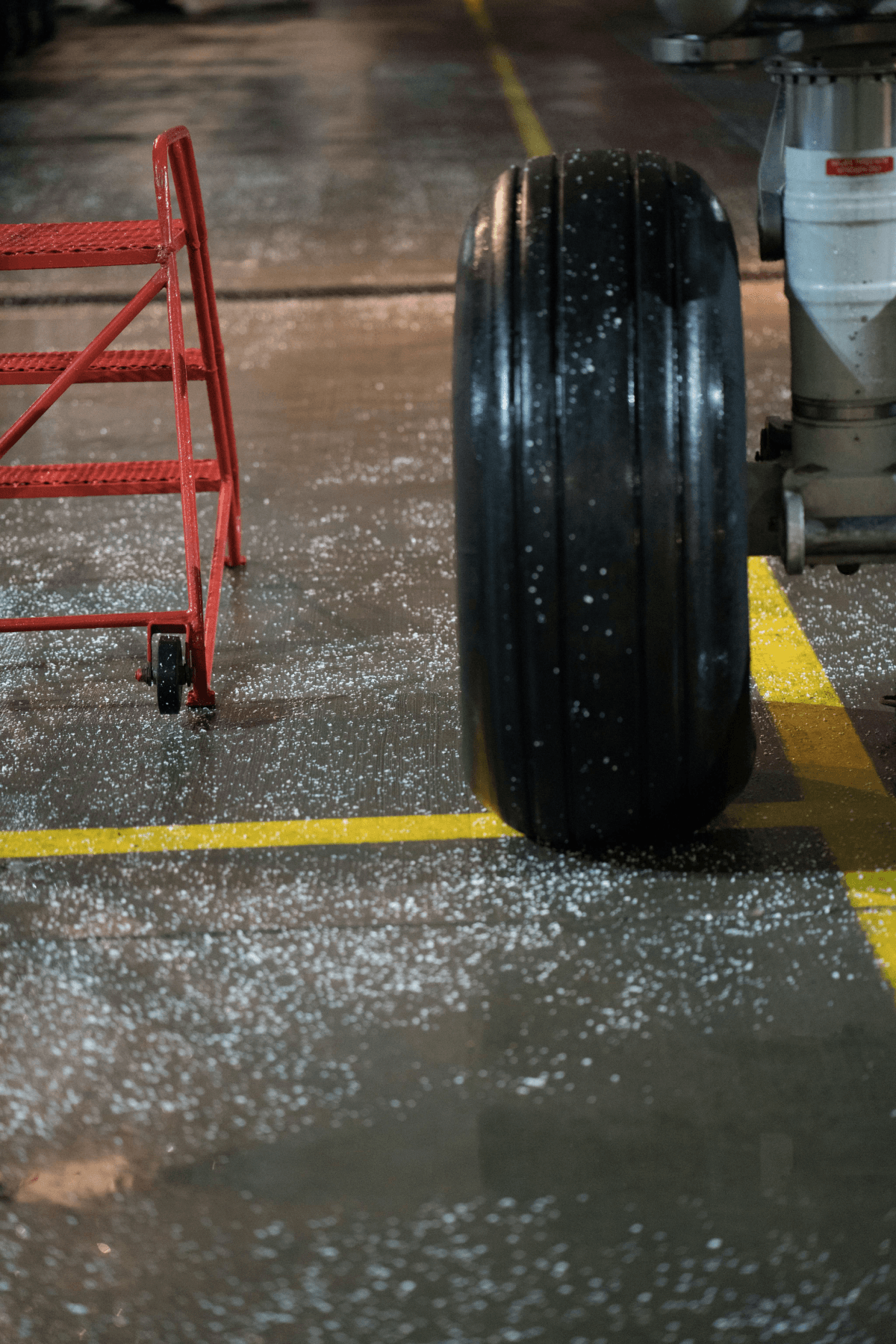
Overview of Haisen's BHM01/02 Surface Friction Tester
Haisen's BHM01/02 Surface Friction Tester is a state-of-the-art device to measure high-friction materials' frictional properties on airport runways. It utilizes advanced technology to accurately assess the surface friction of runway materials, providing crucial data for ensuring safe aircraft operations.
In addition to its advanced technology, the BHM01/02 Surface Friction Tester is also designed for easy operation, making it accessible to airport personnel with varying levels of technical expertise. This user-friendly interface allows for quick and efficient testing, ensuring that runway surfaces can be regularly monitored and maintained to meet safety standards. With its ability to provide real-time data on surface friction, this device offers a proactive approach to runway maintenance, helping airports avoid potential safety hazards and costly disruptions.
Key Features and Specifications of the Friction Testing Equipment
Our cutting-edge airport surface friction tester is a powerful tool for ensuring runway safety. Equipped with precision sensors and a user-friendly interface; it delivers accurate results easily.
The tester’s key features include:
- Precision measurement: Accurately determines both wet and dry surface conditions.
- Portability: Easily transported for quick testing at various airport locations.
- User-friendliness: Intuitive controls and clear display for operators of all skill levels.
Regularly monitoring runway conditions is crucial for preventing accidents. By utilizing this advanced technology, airports can proactively maintain optimal safety standards.
This friction tester is indispensable for any airport prioritizing passenger and aircraft safety.
Advantages of Using Haisen's Surface Friction Tester for Airport Runways
The Haisen BHM01/02 offers numerous advantages, including real-time data collection, portability, and durability. Its ability to quickly assess the coefficient of friction on high-friction surfacing materials makes it an invaluable asset for airport authorities seeking to ensure the safety and performance of their runways.
The Haisen BHM01/02's ability to collect real-time data is a game-changer for airport authorities. This feature allows for immediate assessment and decision-making, ensuring that necessary maintenance or repairs can be promptly carried out to maintain optimal runway safety. Additionally, the tester's portability means that it can be easily transported to different locations within the airport, providing comprehensive coverage for all areas of the runway.
Importance of Coefficient of Friction Test Equipment
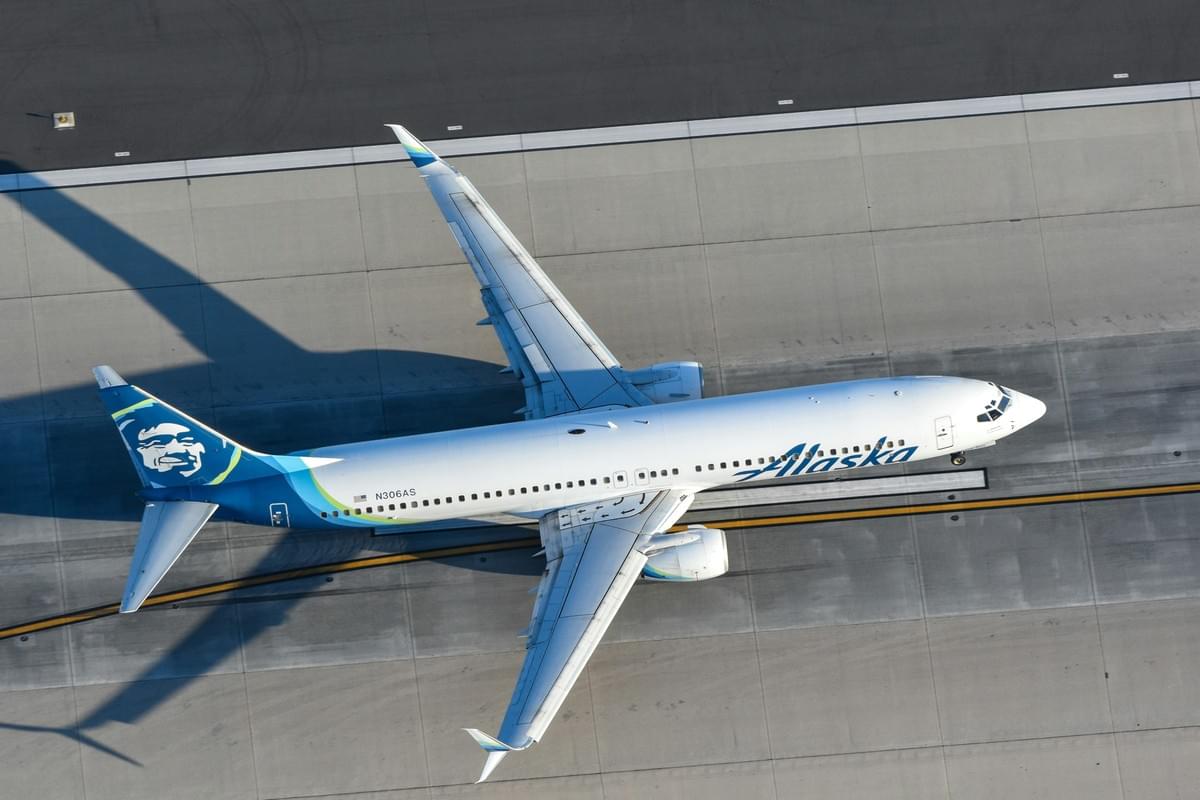
Impact of Coefficient of Friction on Aircraft Braking Performance
High-friction materials play a crucial role in ensuring the safety and efficiency of aircraft braking performance on airport runways. When an aircraft lands, the coefficient of friction between its tires and the runway surface determines how quickly it can come to a stop. High-friction surfaces provide better traction, allowing for shorter braking distances and reducing the risk of skidding or hydroplaning.
High-friction materials are essential for ensuring the safety and efficiency of aircraft braking performance on airport runways. As an aircraft lands, the coefficient of friction between its tires and the runway surface directly impacts its ability to come to a stop. Surfaces with high friction provide better traction, allowing for shorter braking distances and reducing the risk of skidding or hydroplaning. This is crucial for ensuring the safety of passengers and crew and protecting the integrity of the aircraft.
How Friction Sensors Measure and Analyze Surface Friction
Friction sensors are essential components of runway friction testing equipment. They measure and analyze the surface friction between an aircraft's tires and the runway. These sensors use sophisticated technology to accurately assess the coefficient of friction, providing valuable data for airport authorities to make informed decisions about runway maintenance and safety measures.
Furthermore, friction sensors play a critical role in ensuring the safety of aircraft operations by providing real-time data on runway conditions. This allows airport authorities to promptly address issues with low friction, such as rubber buildup from tire wear or contaminants like water, snow, or ice. With access to accurate and up-to-date information, airports can take proactive measures to maintain optimal friction levels and minimize the risk of runway excursions or accidents.
Role of Coefficient of Friction Test Equipment in Ensuring Runway Safety
The coefficient of friction test equipment plays a vital role in ensuring the safety and reliability of airport runways. By regularly testing and monitoring surface friction levels, airport authorities can identify areas that require maintenance or resurfacing with high-friction materials. This proactive approach helps prevent accidents caused by inadequate runway traction, ultimately enhancing overall safety.
In addition to identifying maintenance needs, the coefficient of friction test equipment also allows airport authorities to assess the effectiveness of any friction-enhancing measures that have been implemented. By regularly measuring and analyzing friction levels, airport personnel can determine whether applying high-friction materials or other traction-improving techniques has successfully enhanced runway safety. This data-driven approach ensures that resources are allocated efficiently and effectively, ultimately contributing to the overall reliability of airport operations.
Runway Friction Testing Equipment
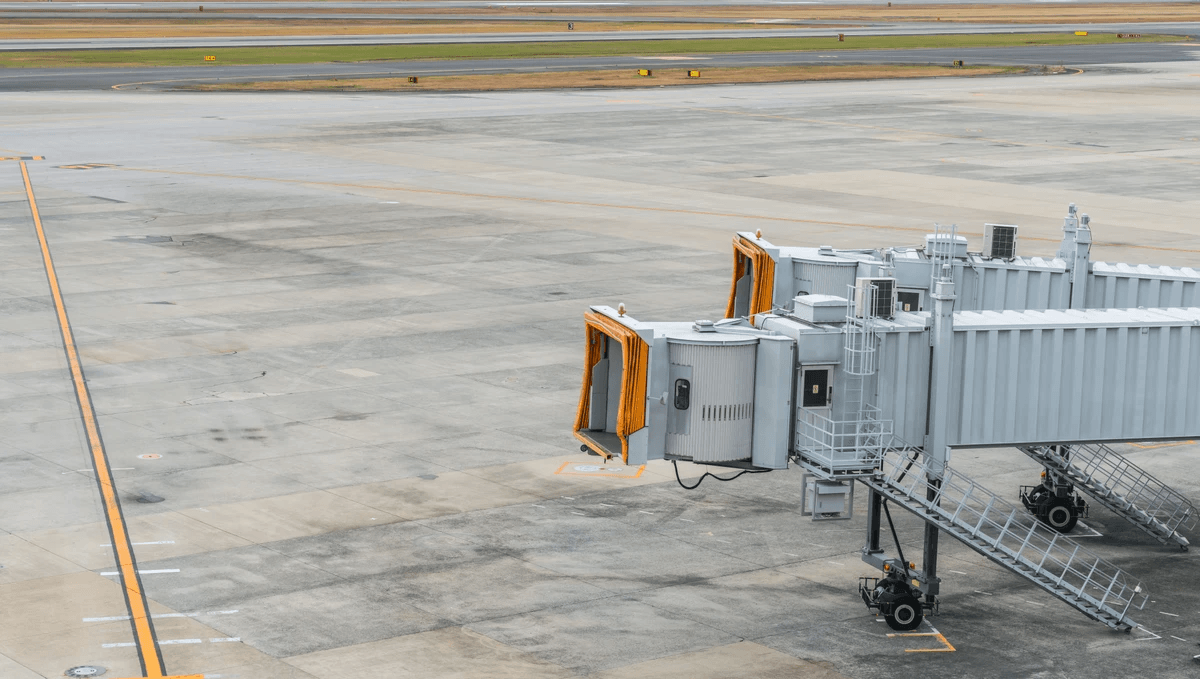
When comparing different types of friction testing equipment for airport runways, it's essential to consider accuracy, portability, and ease of use. The Haisen BHM01/02 Surface Friction Tester stands out for its precision in measuring high-friction material, its compact design for easy transportation, and its user-friendly interface that allows for quick and efficient testing.
Comparison of Different Types of Friction Testing Equipment
Other popular options include the Decagon Devices SKALA Friction Tester and the GripTester GT1. While the SKALA offers advanced data analysis capabilities, the GT1 is known for its durability and reliability in harsh weather conditions. Each model has unique strengths, making it crucial to assess individual needs when selecting the most suitable friction testing equipment.
Factors to Consider When Choosing Runway Friction Testing Equipment
Several factors must be considered when selecting runway friction testing equipment. Primarily, budget, maintenance requirements, and compatibility with existing technology should be taken into account. It is equally important to consider the specific high-friction surfacing materials used on airport runways and to choose equipment capable of accurately measuring their unique properties.
Key factors for selecting runway friction testing equipment include:
- Budgetary constraints
- Maintenance requirements
- Compatibility with existing technology
You can select the most suitable equipment for your airport's needs by carefully evaluating these factors.
Best Practices for Maintaining and Calibrating Friction Testing Equipment
Regular maintenance and calibration of friction testing equipment are vital to ensuring accurate results when testing high-friction surfaces on airport runways. Proper storage in a controlled environment, routine sensor checks, and adherence to manufacturer guidelines for calibration intervals are essential practices to maintain equipment reliability.
Case Studies and Achievements
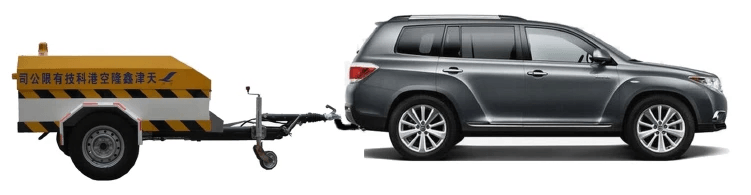
Success Stories of Using High-Friction Materials on Airport Runways
High-friction materials have proven to be a game-changer for airport runways, with success stories from around the world showcasing significant improvements in braking performance and safety. From increased skid resistance to reduced stopping distances, airports using high-friction surfacing have seen remarkable results in enhancing runway safety and performance.
One notable success story comes from a major international airport where high-friction materials were installed on the runway. After the implementation, pilots reported a noticeable improvement in their ability to control the aircraft during landing and takeoff, especially in adverse weather conditions. This translated into increased confidence among flight crews and passengers, who felt safer knowing that the runway was equipped with advanced materials to enhance braking performance.
Impact of Friction Testing on Runway Safety and Performance
The impact of friction testing on runway safety and performance cannot be overstated. By using advanced friction testing apparatus such as the airport surface friction tester, airports can accurately measure and analyze the coefficient of friction on runway surfaces. This allows for proactive maintenance and ensures that runways maintain optimal levels of skid resistance, ultimately leading to safer takeoffs and landings for aircraft.
Furthermore, using high-friction materials in runway construction and maintenance can significantly enhance the effectiveness of friction testing equipment. These materials, such as specially designed asphalt mixtures and grooved runway surfaces, can improve skid resistance and reduce the risk of hydroplaning during wet weather conditions. By incorporating these materials into runway design and maintenance practices, airports can further elevate safety standards and ensure optimal performance for aircraft operations.
Real-World Applications of High-Friction Materials and Friction Testing Equipment
Real-world applications of high-friction materials and friction testing equipment have revolutionized airport operations. With friction sensors and coefficient of friction test equipment, airports can now effectively monitor the condition of their runway surfaces, identify potential hazards, and take corrective actions to maintain safe operating conditions for aircraft. This proactive approach has significantly reduced the risk of runway excursions and improved overall runway safety.
Moreover, high-friction materials and friction testing equipment have also led to more efficient aircraft operations. By accurately measuring the coefficient of friction on runway surfaces, airports can optimize their maintenance schedules and ensure that runways are in optimal condition for takeoffs and landings. This reduces the risk of accidents and minimizes delays and disruptions for airlines and passengers.
Benefits of Investing in High-Friction Materials and Runway Friction Testing Equipment
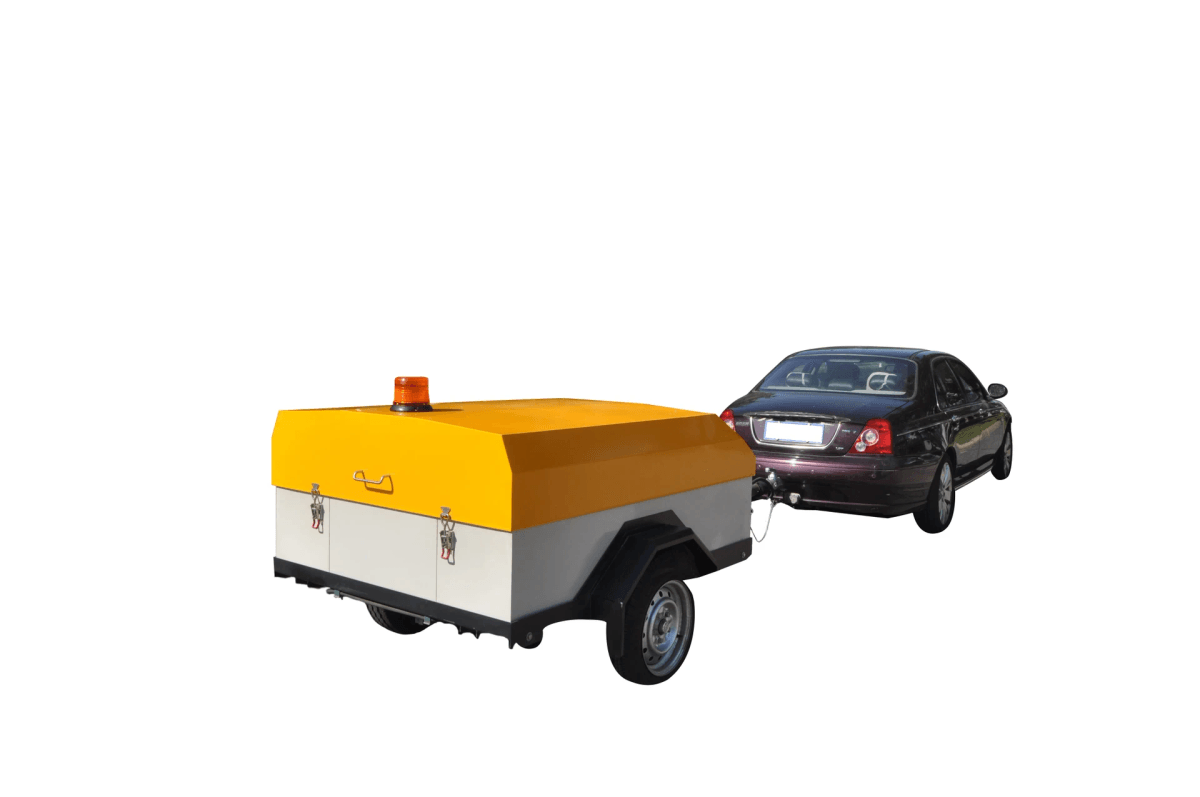
When it comes to ensuring the safety and performance of airport runways, investing in high-friction materials and runway friction testing equipment is crucial. These advancements enhance braking performance, reduce the risk of skidding, and contribute to overall runway safety. As technology continues to evolve, future trends in friction testing will likely focus on improving accuracy and efficiency, further enhancing runway safety.
Ensuring
the Safety and Performance of Airport Runways
By incorporating high-friction materials and utilizing advanced friction testing technology, airports can significantly improve the safety and performance of their runways. High-friction surfacing reduces braking distances and enhances overall aircraft control during takeoff and landing, ultimately minimizing the risk of accidents.
Future Trends in Friction Testing Technology
As technology advances, future friction testing trends will likely focus on improving accuracy, efficiency, and reliability. This includes the development of more sophisticated friction sensors and surface friction testers that provide real-time data on runway conditions. Additionally, advancements in data analysis software will enable airports to make more informed decisions regarding runway maintenance and safety measures.
Investing in high-friction materials such as asphalt with additives or special aggregates can significantly improve runway safety by enhancing surface friction. Additionally, utilizing state-of-the-art coefficient of friction test equipment allows airports to accurately measure surface friction levels, ensuring that runways meet required safety standards. By investing in these technologies, airports can minimize the risk of accidents caused by reduced traction on runway surfaces.