Introduction
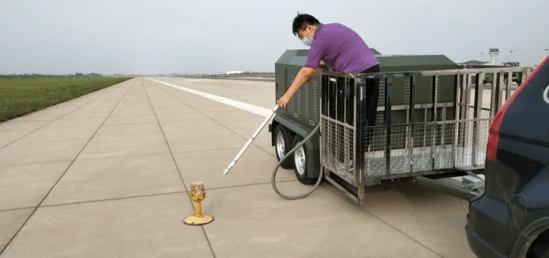
Surface friction testing is crucial for ensuring runway safety in aviation. RFT testing, short for runway friction testing, is pivotal in assessing friction quality on runway surfaces. Friction sensors have emerged as game changers in enhancing runway safety by providing real-time data on surface conditions.
Importance of Surface Friction Testing
Surface friction testing is essential for evaluating the grip and traction of runway surfaces, which directly impacts aircraft safety during takeoff and landing. Regular friction quality tests allow airports to identify low- friction areas and apply high-friction surfacing to enhance safety.
The Role of RFT Testing in Runway Safety
RFT testing is instrumental in identifying runway areas that may pose risks due to low friction levels. This information allows airport authorities to take proactive measures to improve surface conditions, reducing the likelihood of accidents or incidents caused by poor traction.
Friction Sensors: A Game Changer for Runway Safety
Friction sensors have revolutionized runway safety by providing real-time data on surface conditions. This technology enables airports to make informed decisions regarding maintenance and ensure optimal surface conditions for safe aircraft operations.
Friction sensors offer several advantages:
- Real-time monitoring: Continuously measure runway friction levels.
- Early detection: Identify changes in surface conditions promptly.
- Data-driven decisions: Support informed decisions on maintenance and operations.
- Enhanced safety: Contribute to safer takeoffs and landings.
By utilizing friction sensor data, airports can proactively address potential hazards and maintain a high level of runway safety.
The Significance of Surface Friction Testing
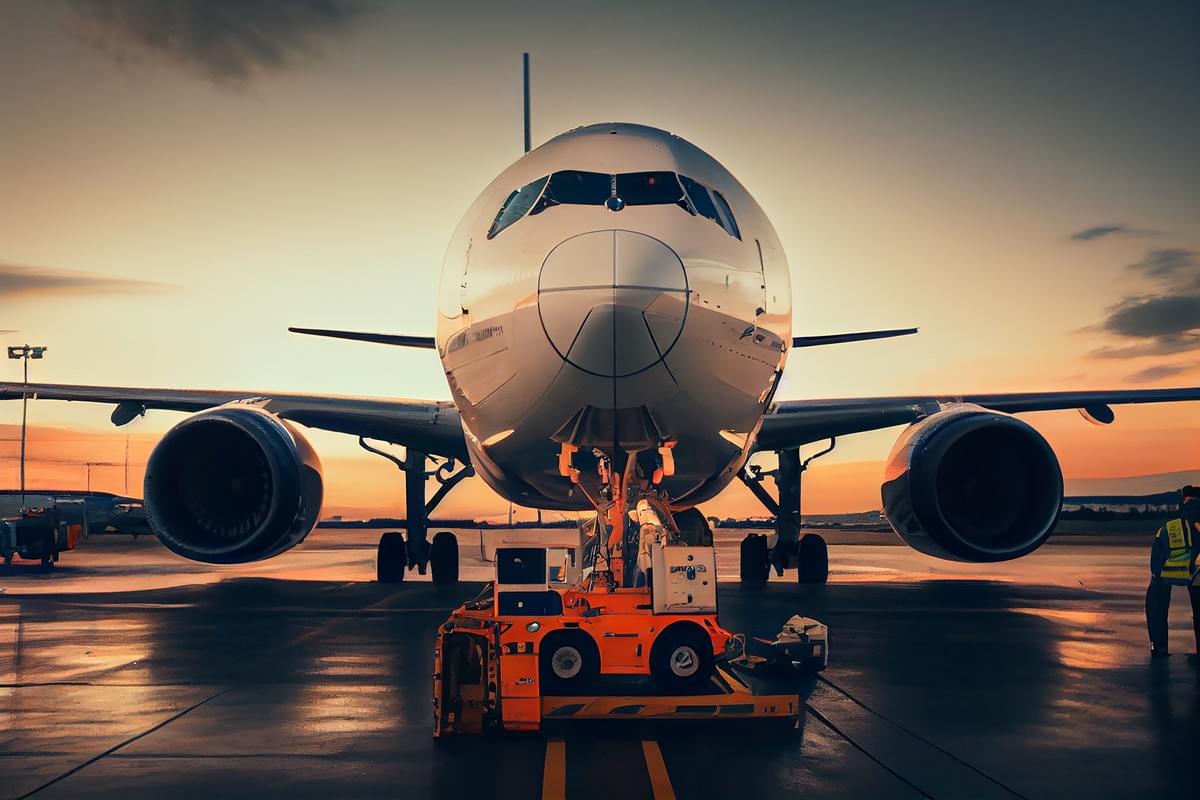
Understanding Surface Friction Testing
Surface friction testing is a crucial process used to measure the frictional properties of runway surfaces, ensuring safe landing and takeoff for aircraft. Surface friction testing provides valuable data to enhance aviation safety by analyzing the interaction between tires and the pavement. High friction surfaces are essential for areas where aircraft need to decelerate quickly, such as at the end of runways or on approach paths. These surfaces are often made of specially designed materials that offer increased grip and reduce the risk of skidding, especially in adverse weather conditions.
Examples of High Friction Surfaces
High-friction surfaces are designed to provide superior grip and skid resistance, especially in adverse weather conditions. Examples include epoxy-based high-friction surfacing, commonly used on airport runways to improve braking performance and reduce the risk of hydroplaning.
Enhancing Runway Safety with Friction Quality Tests
Friction quality tests are vital in maintaining runway safety by identifying areas with inadequate skid resistance. By conducting regular surface friction tests, airports can proactively address potential hazards and ensure optimal conditions for aircraft operations.
Furthermore, surface friction testing allows airports to prioritize maintenance and rehabilitation based on actual data rather than assumptions. This targeted approach helps to optimize resources and minimize downtime for runway repairs, ultimately leading to cost savings for the airport. By investing in regular friction quality tests, airports can demonstrate their commitment to safety and ensure a reliable experience for passengers and airline operators.
The Role of RFT Testing Equipment
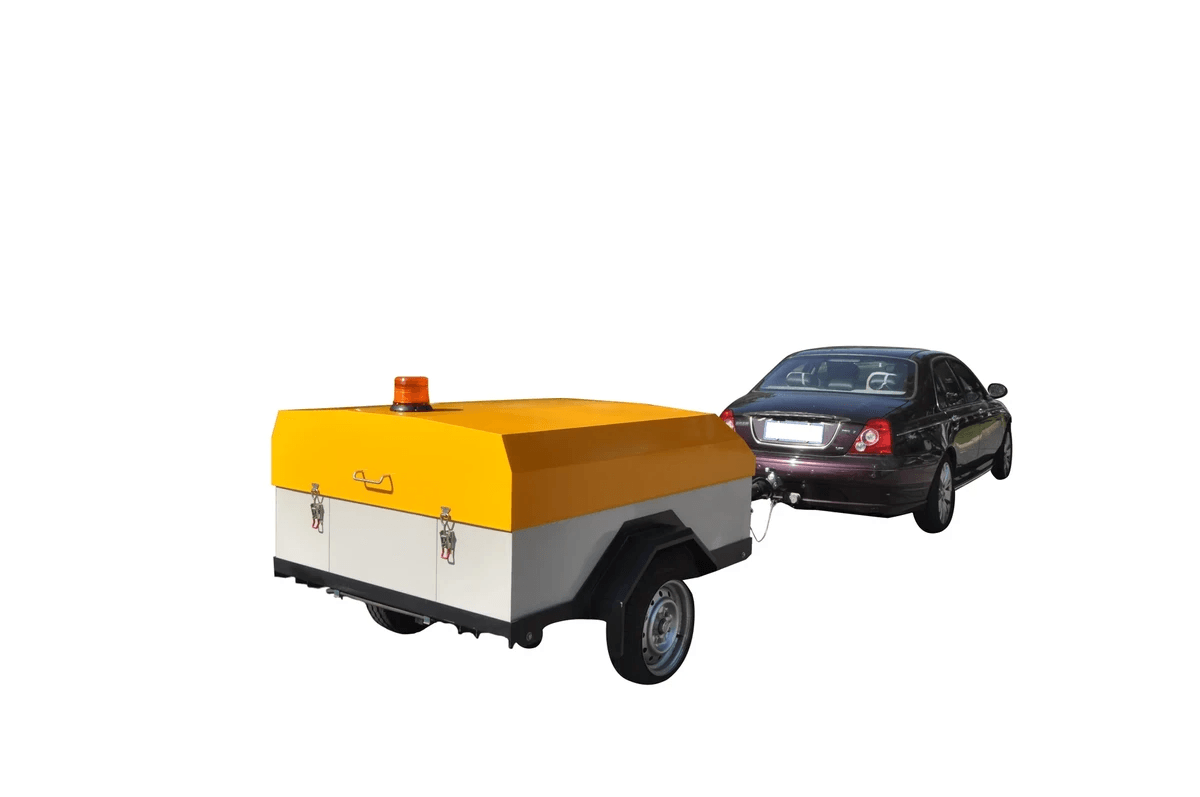
RFT testing equipment ensures runway safety through accurate surface friction testing. The equipment is designed to measure the friction between the tire and the pavement, providing valuable data for assessing runway conditions. This data is essential for airports to make informed decisions about maintenance and safety protocols.
Introducing Haisen's BHM01/02 Surface Friction Tester
Haisen's BHM01/02 Surface Friction Tester is a cutting-edge device engineered explicitly for precise surface friction testing. This tester is equipped with advanced technology and delivers accurate and reliable results, making it an indispensable tool for maintaining safe runway conditions. Its user-friendly interface and portability make it a preferred choice for aviation professionals worldwide.
The BHM01/02 Surface Friction Tester is also designed with safety and reliability features to ensure accurate and consistent results. With built-in quality control mechanisms, this device minimizes the margin of error, providing peace of mind to aviation professionals who rely on its data for crucial decision-making. Furthermore, its durable construction and rigorous testing make it a dependable tool in all weather conditions, contributing to the overall safety of air travel.
Safety and Reliability Features of RFT Testing Equipment
RFT testing equipment boasts safety features that prioritize airport personnel's well-being and ensure test results' reliability. These features include built-in safeguards to prevent accidents during testing procedures and mechanisms to maintain the accuracy of measurements even in challenging weather conditions. With these safety measures in place, airports can trust the data obtained from RFT testing equipment to make critical decisions regarding runway maintenance.
Furthermore, RFT testing equipment is designed with user-friendly interfaces and clear instructions to ensure that airport personnel can operate the equipment safely and effectively. This reduces the risk of human error during testing procedures, leading to more accurate and reliable results. Additionally, the equipment is equipped with real-time monitoring capabilities, allowing personnel to quickly identify and address any issues that may arise during testing, further enhancing the safety and reliability of the process.
The Impact of Friction Sensors on Runway Safety
Friction sensors integrated into RFT testing equipment have revolutionized runway safety by providing real-time data on surface conditions. These sensors continuously monitor friction levels during aircraft landings and takeoffs, alerting airport personnel to any changes that could compromise safety. By leveraging friction sensors, airports can proactively address potential hazards and ensure optimal runway performance.
Benefits of friction sensors in RFT testing equipment include:
- Real-time monitoring: Continuous assessment of runway conditions for immediate response to changes.
- Enhanced safety: Early detection of potential hazards reduces risks for aircraft and passengers.
- Improved operational efficiency: Optimized runway use through proactive maintenance and management.
Accurate calibration of friction sensors is essential for maximizing their impact on runway safety. Proper calibration guarantees precise and reliable data, enabling airport personnel to make informed decisions about runway maintenance and operations. Regular calibration extends the sensors' lifespan, reducing costs and minimizing downtime.
Friction sensors have become indispensable tools for ensuring runway safety. By providing accurate and timely data, these sensors empower airports to proactively manage runway conditions, mitigate risks, and optimize operations.
The Importance of Accurate Calibration
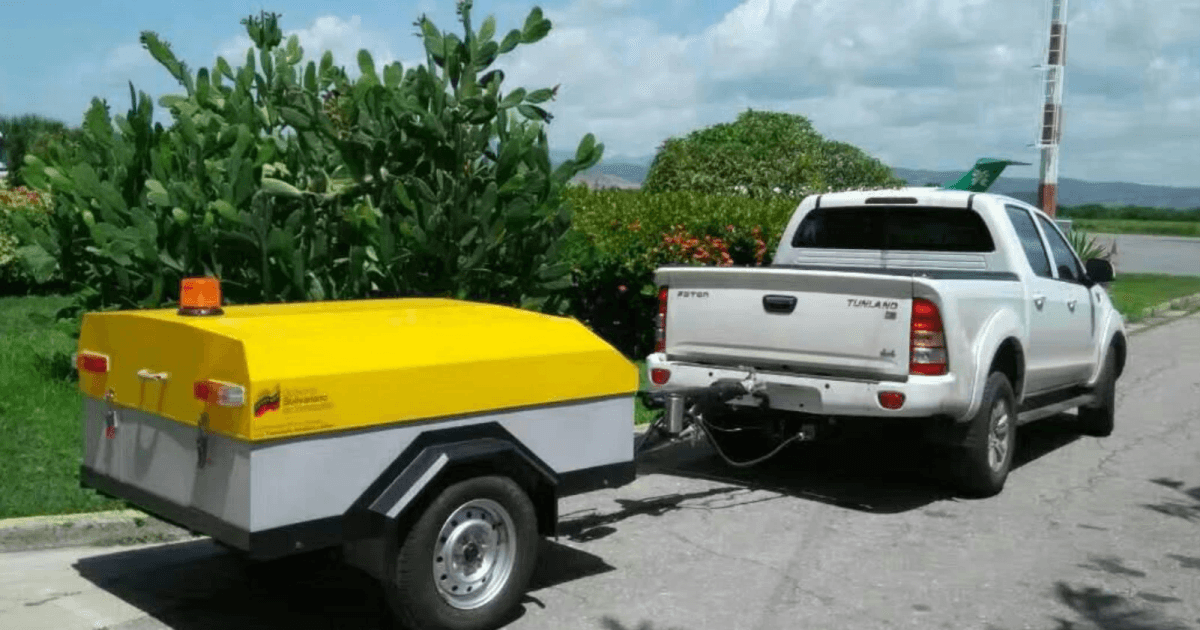
Accurate calibration is crucial for obtaining reliable results in surface friction testing. External electronic calibration ensures precision and consistency in friction measurements, allowing for the identification of potential safety hazards on runways. Without proper calibration, the effectiveness of friction sensors and high-friction surfacing may be compromised, posing a risk to aviation safety.
Ensuring Precision with External Electronic Calibration
External electronic calibration is pivotal in ensuring the accuracy of surface friction testing equipment such as the RFT tester. Calibrating the device with external standards guarantees the measurements are reliable and consistent across different testing conditions. This level of precision is essential for identifying areas with low-friction surfaces that could potentially lead to runway accidents.
External electronic calibration ensures the accuracy of surface friction testing equipment and helps maintain runway safety. Without precise measurements, it would be impossible to identify areas with low-friction surfaces that could potentially lead to accidents. Therefore, investing in external electronic calibration is crucial for airports and aviation authorities to uphold safety standards and prevent runway incidents.
Calibration: A Key Factor in Runway Safety
Calibration is a technical requirement and a key factor in maintaining runway safety. Without accurate calibration, there is a risk of false readings that can lead to incorrect assessments of runway conditions. This can have serious implications for aircraft operations and passenger safety. Therefore, regular calibration checks are essential to ensure that surface friction testing remains an effective tool for enhancing runway safety.
Regular calibration checks are crucial for maintaining the accuracy of surface friction testing equipment. By correctly calibrating the equipment, airport authorities can confidently assess runway conditions and take appropriate measures to enhance safety. Potential hazards could be overlooked without accurate calibration, compromising the safety of aircraft operations and passengers.
The Role of Calibration in Surface Friction Testing
Calibration is the foundation for reliable data collection and analysis in surface friction testing. It ensures that friction sensors accurately measure the interaction between tires and the pavement surface, providing valuable insights into runway conditions. By maintaining precise calibration standards, airports can proactively address potential safety concerns and implement necessary measures to mitigate risks associated with low-friction surfaces.
Additionally, calibration is crucial in ensuring the accuracy and consistency of friction testing results over time. By regularly calibrating the sensors, airports can detect any potential drift or deviation in measurement, allowing for prompt adjustments and maintenance. This proactive approach helps maintain the testing process's integrity and ensures that decision-makers have access to reliable and up-to-date information on runway conditions.
Key Components of RFT Testing
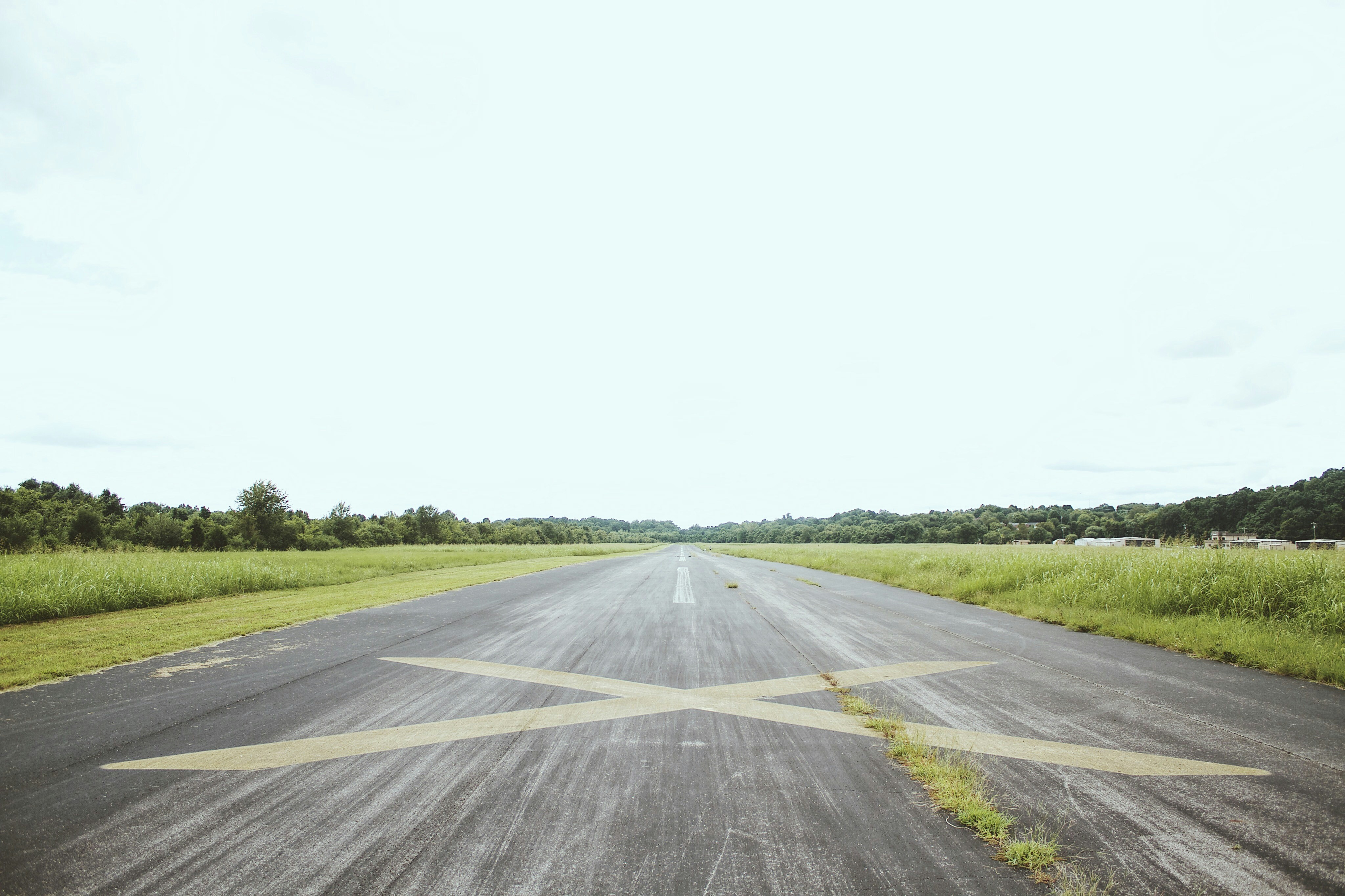
Specialized Tires for Accurate Surface Friction Testing
Regarding surface friction testing, specialized tires ensure accurate and reliable results. These tires are designed with specific tread patterns and rubber compounds that mimic aircraft tires, allowing for realistic friction testing on various surfaces.
Specialized tires are also equipped with computer control systems that allow for continuous testing and provide real-time data on surface friction. This technology enables researchers to make immediate adjustments and fine-tune testing parameters, ensuring the most accurate results. By utilizing specialized tires with advanced control systems, surface friction testing can be conducted with precision and efficiency, ultimately leading to safer and more reliable transportation infrastructure.
Computer Control and Continuous Testing
RFT testing equipment is equipped with advanced computer control systems that enable continuous testing of runway surfaces. This ensures that real-time data is collected and analyzed, providing valuable insights into the runway's friction quality to enhance safety measures.
RFT testing equipment's advanced computer control systems also allow for the customization of testing parameters based on specific runway conditions, such as temperature and moisture levels. This adaptability ensures that the testing process is tailored to the unique characteristics of each runway, providing more accurate and reliable results. Additionally, the real-time data collection and analysis capabilities enable immediate adjustments in response to changing environmental factors, further enhancing the effectiveness of safety measures.
Water System: A Crucial Element for Reliable Testing
The water system integrated into RFT testing equipment is vital for reliable testing. It simulates wet runway conditions, allowing for comprehensive friction tests that account for the environmental factors that impact aircraft performance during landing and takeoff.
Impact and Reach of Surface Friction Testing
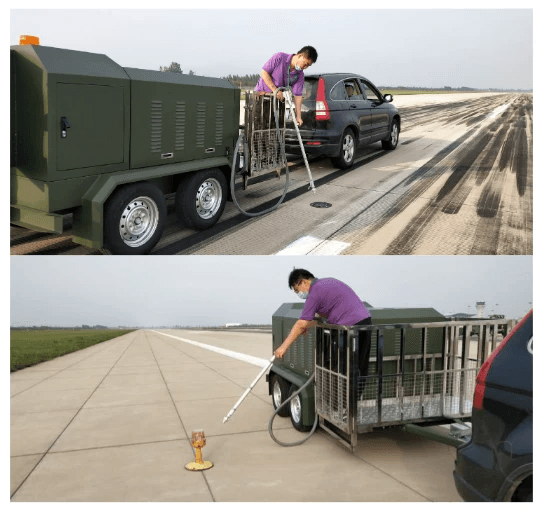
Utilizing Surface Friction Testing in High-Altitude Locations
Surface friction testing is not limited to traditional runway surfaces but has expanded to include high-altitude locations such as mountain airstrips and helipads. Accurate friction data in these challenging environments is crucial for ensuring safe takeoffs and landings, making surface friction testing a valuable tool for aviation safety in diverse terrains.
Surface friction testing in high-altitude locations presents unique challenges due to lower air density, reduced braking effectiveness, and snow or ice. These conditions can significantly impact aircraft performance and require specialized testing equipment to measure surface friction accurately. Haisen's BHM01/02 Surface Friction Tester has been specifically designed to address these challenges, providing aviation professionals with reliable data to make informed decisions about flight operations in mountainous terrain and other high-altitude environments.
Achievements of Haisen's BHM01/02 Surface Friction Tester
Haisen's BHM01/02 Surface Friction Tester has redefined surface friction testing with advanced features like real-time data collection, precise measurement, and a user-friendly interface. Its portability and durability make it the preferred choice for global aviation authorities and airport operators.
Key benefits of the BHM01/02 include:
- Real-time data collection: Enables immediate identification of friction issues.
- Precise measurement capabilities: Provides accurate friction data for informed decision-making.
- User-friendly interface: Simplifies operation and data analysis.
- Portability and durability: Facilitates easy deployment and reliable performance in various conditions.
The BHM01/02 enhances runway safety and maintenance by offering efficient and accurate friction testing. This has led to a reduction in runway accidents, prioritizing passenger and crew well-being.
Haisen's BHM01/02 Surface Friction Tester is a testament to the company's commitment to aviation safety and technological innovation.
The Global Impact of Surface Friction Testing
The global impact of surface friction testing cannot be overstated, as it plays a pivotal role in enhancing runway safety worldwide. By providing essential data on surface conditions, friction sensors have reduced the risk of runway excursions and enhanced overall flight safety. With advancements in technology and continuous research, the impact of surface friction testing is set to expand further, benefiting aviation safety on a global scale.
With the increasing frequency of extreme weather events, such as heavy rain and snow, surface friction testing becomes even more critical in ensuring runway safety. By accurately measuring the friction levels on the runway surface, airports can proactively address potential hazards caused by adverse weather conditions. This proactive approach reduces the likelihood of accidents and minimizes flight delays and cancellations, ultimately benefiting passengers and airlines.
The Future of Friction Sensors in Aviation Safety
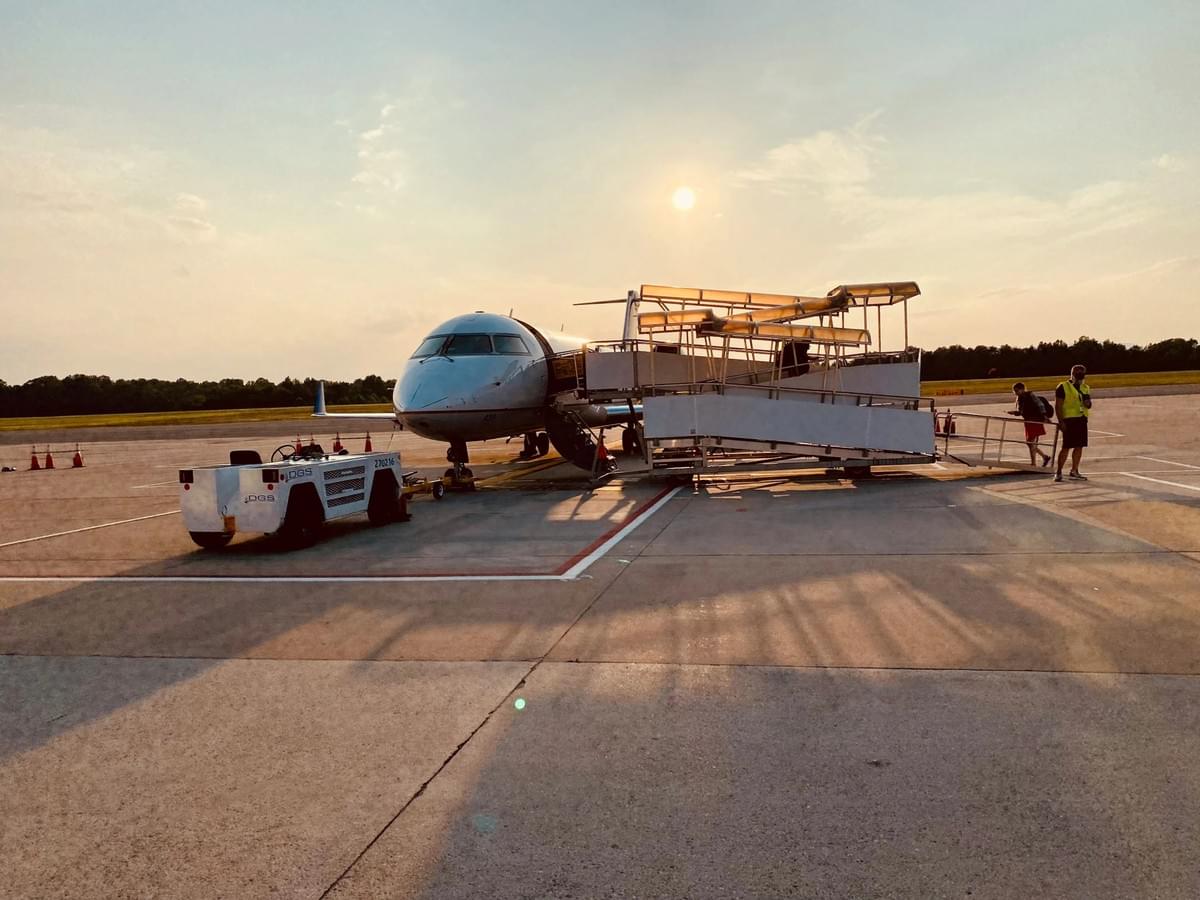
Surface friction testing is crucial in enhancing runway safety by providing valuable data on the surface's condition. RFT testing, or surface friction testing, is instrumental in identifying high-friction surfaces that contribute to safer landings and takeoffs. Friction sensors are revolutionizing aviation safety by allowing real-time monitoring of runway conditions, leading to advancements in friction quality tests.
Enhancing Runway Safety with Surface Friction Testing
By conducting regular surface friction tests, airports can ensure that their runways meet the necessary safety standards for aircraft operations. High friction surfacing, such as grooved or textured pavements, significantly improves skid resistance and reduces the risk of accidents during adverse weather conditions. Friction quality tests enable airports to maintain optimal runway conditions and prevent potential hazards.
Integrating friction sensors into runway maintenance and management systems represents the future of aviation safety. These sensors provide real-time data on surface conditions, allowing airports to address issues affecting aircraft operations proactively. As technology advances, friction sensors will play an increasingly vital role in ensuring the safety and efficiency of air travel.
Advancements in Surface Friction Testing
Recent advancements in surface friction testing equipment have led to more accurate and reliable results, enabling airports to make informed decisions regarding runway maintenance and improvements. Developing specialized tires for precise testing, computer-controlled systems for continuous monitoring, and water systems for reliable testing have all contributed to significant advancements in surface friction testing.
With its ability to enhance runway safety, the future potential of friction sensors in aviation safety, and ongoing advancements in surface friction testing equipment, it is clear that surface friction testing will continue to be a critical component of ensuring safe aircraft operations worldwide.