Introduction
When it comes to industrial automation, the electric rotary actuator plays a crucial role in providing rotational power for various applications. But what exactly is an electric rotary actuator? This innovative device is a type of rotational power actuator that converts electrical energy into mechanical motion, allowing for precise control and movement in industrial settings. The importance of rotary electrical actuators cannot be understated, as they offer numerous benefits and advantages over traditional actuation methods.
Understanding the Electric Rotary Actuator
An electric rotary actuator is a device that translates electrical energy into rotary motion, making it ideal for controlling valves and dampers in industrial processes. With its ability to provide precise and reliable movement, this type of actuator has become an essential component in modern industrial automation systems.
The Importance of Rotary Electrical Actuators
Rotary electrical actuators are vital for ensuring efficient and accurate control over various processes in industries such as oil and gas, water treatment, and manufacturing. Their ability to deliver consistent performance and precise positioning makes them indispensable for maintaining operational efficiency and safety.
Benefits of Utilizing a Part-Turn Valve Electric Actuator
One of the key advantages of using a part-turn valve electric actuator is its versatility in controlling valves that require only partial rotation, such as ball valves or butterfly valves. This type of actuator offers greater control precision, reduced maintenance requirements, and improved operational reliability compared to traditional pneumatic or hydraulic actuators.
What Does an Electric Rotary Actuator Do?
An electric rotary actuator is a device that converts electrical energy into rotational power, allowing for precise control of valve and damper positions in industrial settings. This type of actuator is commonly used to automate the operation of valves in various applications, such as oil and gas, water treatment, and HVAC systems.
The Functionality and Purpose
Electric rotary actuators are designed to provide smooth and accurate rotational movement, allowing for precise positioning of valves and dampers. By utilizing electrical power, these actuators can deliver consistent torque output, ensuring reliable operation in critical industrial processes. Their primary purpose is to automate the control of flow rates, pressure levels, and temperature within pipelines and ducts.
Electric rotary actuators are widely used in various industries such as oil and gas, water and wastewater treatment, power generation, and chemical processing. In the oil and gas industry, these actuators play a crucial role in controlling the flow of crude oil, natural gas, and other fluids through pipelines. They ensure precise positioning of valves to regulate the flow rates and pressure levels, contributing to the efficient operation of oil refineries and natural gas processing plants.
Applications in Different Industries
Electric rotary actuators are widely used across a range of industries due to their versatility and reliability. They are commonly employed in oil refineries for controlling the flow of crude oil through pipelines, as well as in power plants for regulating steam or cooling water flow. Additionally, these actuators play a crucial role in municipal water treatment facilities by managing the movement of water through distribution systems.
Electric rotary actuators are also widely used in the automotive industry for controlling various functions in vehicles, such as adjusting the position of mirrors, opening and closing convertible roofs, and regulating air flow in HVAC systems. Their precise and efficient operation makes them an ideal choice for enhancing the performance and functionality of modern automobiles. Furthermore, these actuators are utilized in aerospace applications to control the movement of aircraft components, such as flaps, landing gear, and engine cowlings, ensuring safe and reliable operation during flight.
Advantages Over Traditional Actuators
Compared to traditional pneumatic or hydraulic actuators, electric rotary actuators offer several advantages. They are more energy-efficient, providing precise control without the need for additional air compressors or hydraulic pumps. Electric actuators also offer greater flexibility in terms of speed control and positioning accuracy, making them ideal for applications that require fine-tuned adjustments.
In addition, electric rotary actuators are easier to install and maintain compared to their pneumatic or hydraulic counterparts. With fewer components and simpler control systems, electric actuators require less maintenance and downtime, ultimately reducing overall operational costs. This ease of installation and maintenance makes electric actuators a more convenient and cost-effective option for many industrial applications.
Haisen's Part-Turn Valve Electric Actuator
Haisen's part-turn valve electric actuator is a cutting-edge solution for industrial automation, offering a range of features and specifications that make it stand out in the market. With robust construction and high-quality materials, this electric actuator ensures durability and reliability in demanding industrial environments.
Features and Specifications
The Haisen part-turn valve electric actuator boasts a compact design with a powerful motor that delivers precise and efficient rotational power. Equipped with advanced control systems, it offers accurate positioning and torque control, making it suitable for various valve applications. Its modular construction allows for easy maintenance and upgrades, ensuring long-term performance and cost savings.
Furthermore, the Haisen part-turn valve electric actuator is designed for seamless integration with remote control systems, allowing for easy and convenient operation from a distance. This feature enhances safety by minimizing the need for manual intervention in potentially hazardous environments, while also improving overall efficiency and productivity. With its user-friendly interface and compatibility with various communication protocols, this actuator offers unparalleled flexibility in valve control applications.
Remote Control Capabilities
One of the key advantages of Haisen's electric actuator is its remote control capabilities, enabling operators to monitor and adjust valve positions from a distance. This feature not only enhances operational efficiency but also improves safety by reducing the need for manual intervention in hazardous or hard-to-reach areas of industrial facilities.
Versatility in Industrial Applications
Haisen's part-turn valve electric actuator is designed to be versatile, catering to a wide range of industrial applications such as water treatment plants, oil refineries, chemical processing facilities, and power generation stations. Its adaptability to different valve types and sizes makes it an ideal choice for industries seeking reliable automation solutions.
The Efficiency of Electric Actuators
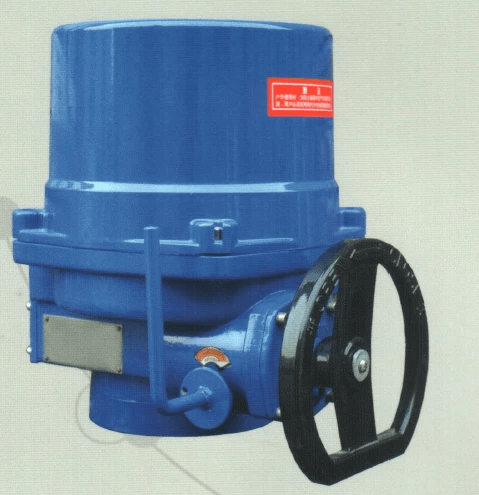
Energy Efficiency and Cost Savings
Electric rotary actuators are known for their energy efficiency, consuming less power compared to traditional pneumatic or hydraulic actuators. This results in significant cost savings for industries, as they require less energy to operate, reducing overall operational expenses.
Electric rotary actuators also contribute to environmental benefits by reducing carbon emissions. With their energy efficiency, these actuators help industries lower their carbon footprint, making them a more sustainable choice for businesses looking to minimize their environmental impact. By utilizing electric rotary actuators, companies can align with green initiatives and demonstrate their commitment to environmental responsibility.
Environmental Benefits
The use of electric rotary actuators also brings environmental benefits, as they produce zero emissions during operation. This makes them an eco-friendly choice for industrial automation, contributing to a cleaner and greener environment for future generations.
In addition to producing zero emissions during operation, electric rotary actuators also have a longer lifespan compared to traditional pneumatic or hydraulic systems. This long-term reliability reduces the need for frequent replacements and maintenance, further minimizing the environmental impact of industrial automation. By choosing electric rotary actuators, companies can not only reduce their carbon footprint but also save resources in the long run.
Long-Term Reliability
One of the key advantages of electric rotary actuators is their long-term reliability. With fewer moving parts and minimal wear and tear, these actuators offer a longer lifespan compared to their traditional counterparts, reducing maintenance costs and downtime for industrial processes.
Electric rotary actuators also offer precise control and positioning, making them ideal for applications that require accurate and consistent movement. This level of precision helps to improve overall efficiency and productivity in industrial processes, allowing for more streamlined operations and higher quality output. By minimizing the risk of errors or malfunctions, these actuators contribute to a more reliable and dependable production environment.
Common Problems with Actuators
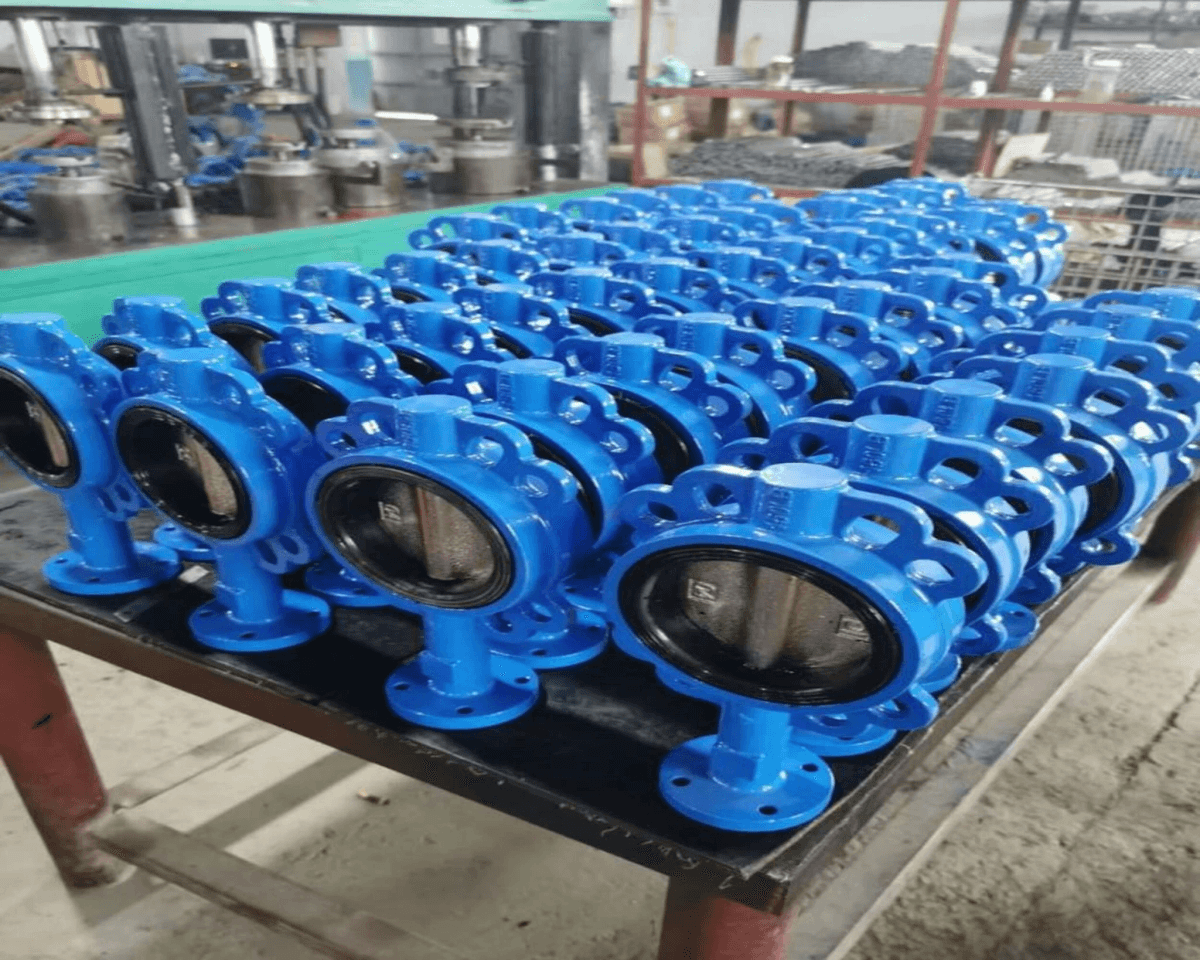
Potential Issues and Troubleshooting
One common problem with electric rotary actuators is the occurrence of mechanical failures due to wear and tear over time, resulting in decreased performance and functionality. Troubleshooting this issue involves conducting regular inspections to identify any signs of wear, such as unusual noises or vibrations during operation, and addressing them promptly to prevent further damage.
Maintenance Best Practices
To ensure the efficient operation of rotary electrical actuators, regular maintenance is essential. This includes lubricating moving parts, checking for loose connections or worn-out components, and cleaning the actuator to prevent the buildup of dirt or debris that can hinder its performance. By following these best practices, potential issues can be minimized, prolonging the lifespan of the actuator.
Extending the Lifespan of Electric Actuators
The key to extending the lifespan of electric actuators lies in proactive maintenance and proper care. Implementing a preventive maintenance schedule that includes routine inspections and servicing can help identify potential problems early on and prevent costly breakdowns. Additionally, using high-quality components and following manufacturer recommendations for operating conditions can contribute to maximizing the longevity of rotary electrical actuators.
By implementing these maintenance best practices and troubleshooting potential issues promptly, users can ensure that their electric rotary actuators operate at optimal efficiency for an extended period while minimizing downtime and repair costs.
Choosing the Most Efficient Type of Actuator
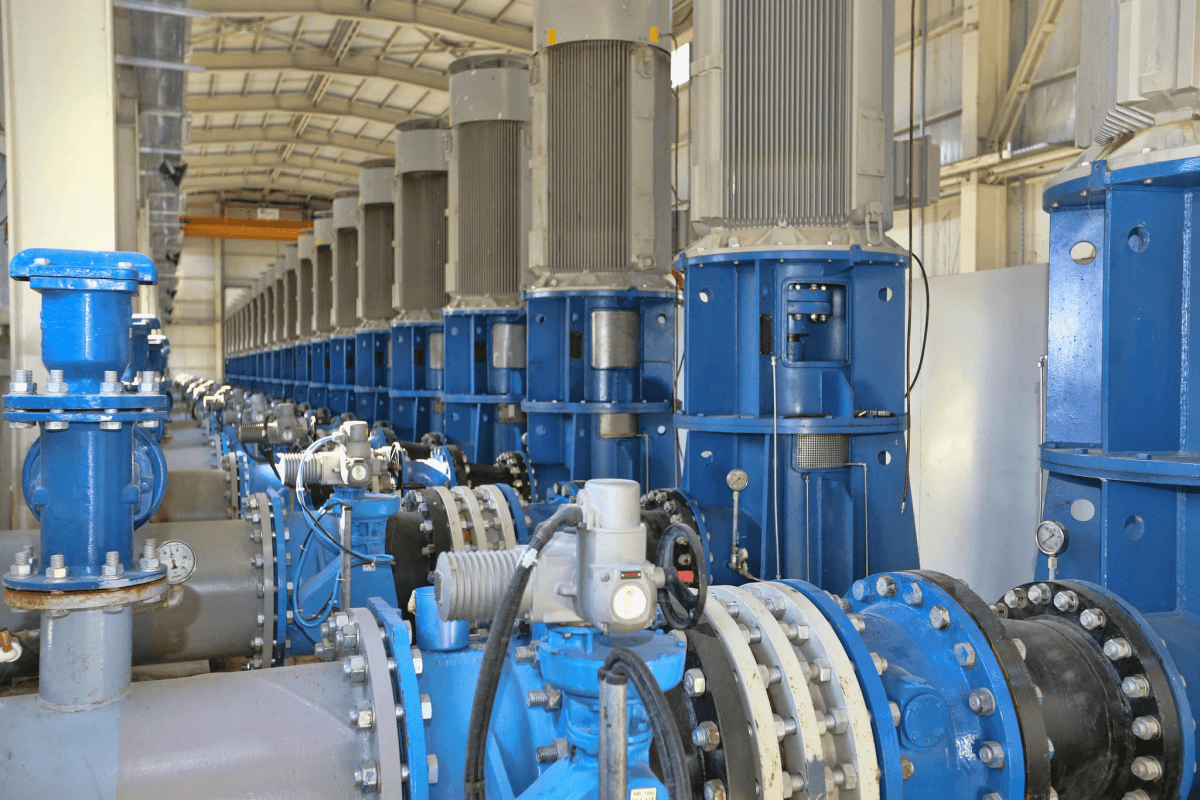
When considering the most efficient type of actuator for your industrial needs, there are several factors to take into account. The size and weight of the valve, the required torque and speed, and the environmental conditions in which the actuator will operate all play a crucial role in determining the most suitable option for your application.
Factors to Consider
The size and weight of the valve that needs to be actuated is an important consideration when choosing an electric rotary actuator. The torque and speed requirements also need to be carefully evaluated to ensure that the actuator can meet the demands of your specific application. Additionally, environmental factors such as temperature, humidity, and exposure to corrosive substances must be taken into account to select an actuator that can withstand these conditions.
When considering an electric rotary actuator, it is also important to think about the power supply available for the actuator. Whether it is a 12V DC, 24V DC, or 120V AC power source, ensuring that the actuator is compatible with the available power supply is crucial for seamless integration into your system. Additionally, factors such as mounting options and space constraints should be taken into account to ensure that the actuator can be installed in the desired location without any issues. Taking these factors into consideration will help you select an electric rotary actuator that best fits your specific needs.
Customization Options
One of the key advantages of electric rotary actuators is their ability to be customized according to specific requirements. From different mounting options to various control options such as on/off or modulating control, electric actuators offer a wide range of customization possibilities. This allows for tailored solutions that can optimize performance and efficiency in diverse industrial settings.
Electric rotary actuators can also be customized in terms of speed and torque, allowing for precise control over the movement of industrial equipment. This level of customization ensures that the actuators can meet the specific demands of different applications, whether it's a high-speed operation or a heavy-duty task. By fine-tuning the speed and torque, users can maximize performance and productivity in their specific industrial settings.
Maximizing Performance in Specific Applications
Electric actuators provide versatility in terms of performance optimization for specific applications. By selecting an actuator with features such as adjustable speed control or fail-safe functionality, it is possible to maximize performance based on unique operational needs. This adaptability ensures that electric rotary actuators can effectively meet a wide range of industrial requirements.
Electric actuators with adjustable speed control allow for precise and customized operation, ensuring that the actuator performs at its optimal level for specific applications. This level of control enables users to fine-tune the speed of the actuator to match the exact requirements of the task at hand, resulting in improved efficiency and productivity. By having the ability to adjust speed as needed, electric actuators can deliver superior performance in a wide range of industrial settings.
Conclusion
Electric rotary actuators are revolutionizing industrial automation with their efficiency and versatility. Embracing innovation in industrial automation means taking advantage of the benefits of electric actuators, such as energy efficiency, remote control capabilities, and long-term reliability. As technology continues to advance, the future of electric actuators in industrial settings looks promising, offering enhanced performance and cost savings for various applications.
Maximizing Efficiency with Electric Rotary Actuators
Electric rotary actuators play a crucial role in maximizing efficiency in industrial processes by providing precise and reliable control over part-turn valves. Their ability to deliver rotational power with minimal energy consumption makes them an ideal choice for industries looking to optimize their operations while reducing costs. With remote control capabilities and customizable features, electric rotary actuators offer a level of efficiency that traditional actuation methods cannot match.
Embracing Innovation in Industrial Automation
As industries continue to evolve, embracing innovation in industrial automation becomes imperative for staying competitive and meeting growing demands. Electric rotary actuators represent a significant leap forward in automation technology, offering improved performance, reduced maintenance requirements, and enhanced safety features. By integrating these advanced actuators into their systems, businesses can streamline their processes and adapt to changing industry standards.
The Future of Electric Actuators in Industrial Settings
The future of electric actuators in industrial settings is bright as advancements in technology continue to drive innovation. With ongoing developments aimed at improving efficiency, reliability, and adaptability, electric rotary actuators are poised to become even more integral to various industries. Their potential to contribute to sustainable practices by reducing energy consumption aligns with the growing focus on environmental responsibility within industrial sectors.