Introduction
Electrical actuators are crucial in automating industrial processes, providing precise control and efficient operation. These versatile devices are used in various applications, including actuator valves, electric valve actuators, and motorized actuators, offering seamless integration with various systems. It is essential to understand the diverse applications of these actuators and the importance of selecting the right one for specific needs.
Understanding the Role of Electrical Actuators
Electrical actuators are essential components in various industrial applications, particularly in controlling the flow of fluids and gases.
Key applications of electrical actuators:
- Valve control: Electrical actuators are widely used in actuator valves to regulate the opening and closing of valves, ensuring precise control of fluid and gas flow.
- HVAC systems: Electrical actuators control dampers, louvers, and other components, enabling efficient airflow management and temperature regulation.
- Other industrial processes: Electrical actuators are used in numerous other industrial processes, such as material handling, robotics, and factory automation, where precise positioning and movement are required.
Electrical actuators offer versatility, reliability, and precise control, making them indispensable in various industrial applications. Their ability to efficiently regulate fluid and gas flow and control various mechanical components contributes to improved productivity, safety, and energy efficiency.
Exploring the Diversity of Actuator Applications
Electrical actuators' versatility is evident in their widespread applications across various industries. From manufacturing and energy production to water treatment and transportation, they are utilized for tasks ranging from simple on/off control to complex motion sequences. Their adaptability makes them indispensable in modern industrial automation.
Electrical actuators are designed to meet the specific needs of each industry, providing precise and reliable control over a wide range of applications. Whether automating heavy machinery's movement in manufacturing or regulating water flow in treatment plants, these actuators offer unparalleled flexibility. Their ability to seamlessly integrate with various systems and equipment makes them a go-to choice for engineers and automation specialists looking to optimize their processes.
Importance of Choosing the Right Actuator for Specific Needs
The appropriate electrical actuator is crucial for achieving desired outcomes in industrial processes. Factors such as load capacity, speed, environmental conditions, and compatibility with existing systems must be carefully considered when choosing an actuator. The right selection ensures optimal performance, reliability, and cost-effectiveness.
Now that we have explored electrical actuators' fundamental role and diversity let's delve deeper into specific types, such as Haisen's Part-Turn Valve Electric Actuator and linear and rotary actuators, to understand their features, benefits, limitations, and real-world applications.
The QT Series Part-Turn Valve Electric Actuator
The QT series part-turn valve electric actuator by Haisen is a cutting-edge product designed to control actuator valves precisely. With features like remote operation and 90° rotation capability, this electric actuator offers unparalleled versatility for controlling butterfly, ball, and plug valves. It is a game-changer in the industrial automation sector.
Features and
Specifications of Haisen's Part-Turn Valve Electric Actuator
Haisen's QT series part-turn valve electric actuator boasts a robust design, high torque output, and exceptional durability. It is equipped with advanced technology for precise positioning and smooth operation. With local or remote control options, this electric actuator provides unmatched flexibility for valve control in various industrial applications.
Also, Haisen's QT series part-turn valve electric actuator is designed to withstand harsh environmental conditions, making it suitable for use in various industrial fields such as oil and gas, water treatment, and power generation. Its robust construction ensures reliable performance even in demanding applications, providing operators and maintenance teams peace of mind. This level of durability makes it a cost-effective solution for long-term valve control needs.
Application of this Actuator in Various Industrial Fields
This innovative electric actuator has found widespread application across diverse industrial sectors such as petrochemical, metallurgy, shipbuilding, food processing, and power generation. Its ability to seamlessly integrate with different types of valves makes it an ideal choice for industries that rely on efficient flow control systems.
Furthermore, the actuator's compact design and high torque output suit tight spaces and heavy-duty applications. This versatility allows industries to optimize operational efficiency and minimize downtime, resulting in significant cost savings. The actuator's advanced control features also enable precise and reliable valve positioning, ensuring consistent product quality and regulatory compliance in various industrial processes.
Benefits of Using this Specific Actuator for Valve Control
The Haisen QT series part-turn valve electric actuator is valuable for industries seeking to enhance operational efficiency and safety.
- Precision Control: Ensures optimal performance of actuated valves, minimizing downtime and maximizing productivity.
- Durability: Designed to withstand harsh industrial environments, ensuring long-term reliability and reducing equipment failures.
- Enhanced Safety: Robust construction and advanced technology minimize the risk of valve malfunctions or accidents.
By investing in the Haisen QT series electric actuator, businesses can significantly improve operational efficiency, reduce maintenance costs, and enhance safety measures. This cutting-edge technology is a valuable addition to any industrial automation process.
Linear Actuators
Linear actuators are essential in various automotive, medical, and manufacturing industries. They come in different types, such as electric, pneumatic, and motorized actuators, each serving a specific purpose. For instance, electric valve actuators are commonly used in industrial settings for precise valve control.
Different Types and Uses of Linear Actuators in Various Industries
In the automotive industry, linear actuators adjust car seats and convertible roofs. They play a crucial role in hospital beds and patient lifts in the medical field. In manufacturing, linear actuators are utilized in conveyor systems and robotic assembly lines.
In aerospace, linear actuators are used in aircraft seating and cargo handling systems. The precise and reliable movement provided by linear actuators is essential for ensuring passenger comfort and safety, as well as efficient cargo loading and unloading. Additionally, linear actuators are used to deploy landing gear and other critical systems, contributing to the overall performance and functionality of aircraft.
Advantages and Disadvantages of Linear Actuators
One advantage of linear actuators is their ability to provide precise positioning control with high accuracy. However, a potential disadvantage is their slower speed than rotary actuators. It's important to consider these factors when choosing the most suitable actuator for specific applications.
Another advantage of linear actuators is their ability to provide consistent and repeatable motion, making them ideal for applications that require precise and reliable movement. Additionally, linear actuators are often more compact and easily integrated into existing systems, saving space and simplifying installation. However, it's important to note that linear actuators may require more maintenance due to the complex mechanical components involved in their operation.
How to Select the Most Suitable Linear Actuator for Specific Applications
Factors such as load capacity, speed requirements, and environmental conditions must be considered when selecting a linear actuator. For instance, an electric actuator may be the best choice if an application requires high-speed movement with low force requirements.
In contrast, if the application requires high force and precision control, a hydraulic actuator might be more suitable because it can handle heavy loads and provide smooth, controlled movement. Environmental conditions such as temperature, moisture, and exposure to chemicals should also be considered when selecting a linear actuator. A rugged and durable actuator with protective seals and coatings may be necessary for applications in harsh environments to ensure reliable performance over time.
Rotary Actuators
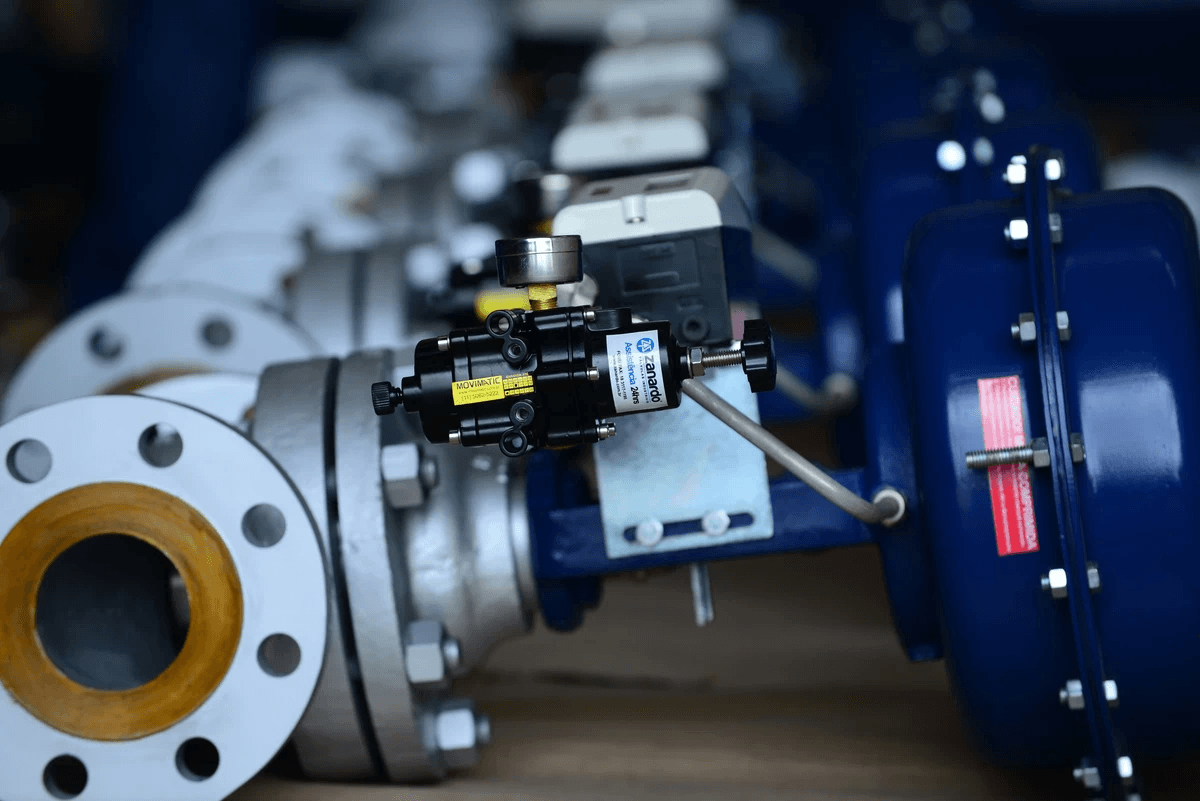
Rotary actuators are essential in industrial automation, providing rotational motion to control various devices and machinery. These actuators are commonly used in applications such as conveyor systems, robotic arms, and assembly lines, where precise and controlled rotation is required for optimal performance.
Exploring the Functionality and Applications of Rotary Actuators
Rotary actuators operate by converting energy into rotational motion, allowing them to control the movement of valves, dampers, and other mechanical components. They are widely utilized in manufacturing, automotive, and aerospace industries for tasks that involve rotating equipment or controlling flow direction within pipelines.
Rotary actuators offer several advantages, such as their compact size and ability to generate high torque, making them ideal for applications where space is limited or a strong rotational force is required. Additionally, these actuators can be customized to suit specific requirements, allowing for greater flexibility in design and implementation. However, it's important to note that rotary actuators also have limitations, such as the potential for wear and tear over time, which can affect their overall performance and reliability.
Understanding the Advantages and Limitations of Rotary Actuators
Rotary actuators offer a compelling solution for applications requiring high torque output in a compact form factor. Their efficiency and versatility make them a popular choice in various industries.
Here are some key advantages and considerations:
- High Torque Output: Rotary actuators deliver substantial torque, making them ideal for heavy-duty tasks.
- Compact Size: Their compact design allows for integration into space-constrained environments.
- Efficient Energy Consumption: Rotary actuators often exhibit efficient power usage, reducing operating costs.
- Bi-directional Rotation: They can rotate in both directions, enabling application flexibility.
- Potential Limitations: While offering numerous benefits, rotary actuators may have limitations in speed control and precision positioning compared to linear actuators.
Careful consideration of these factors is essential when selecting rotary actuators for specific applications. Engineers can make informed decisions to optimize their designs by understanding their strengths and potential drawbacks.
Real-World Examples of Rotary Actuators in Action
In the petrochemical industry, rotary actuators control valve operations in oil refineries and chemical processing plants. For example, Haisen's QT series part-turn valve electric actuator is employed for precisely 90° rotation control of butterfly and ball valves in these critical industrial settings. This ensures efficient flow regulation and enhances overall operational safety.
Rotary actuators are widely used in the petrochemical industry and the automotive manufacturing sector. They control the movement of robotic arms and conveyor belts on assembly lines. By employing rotary actuators, automotive manufacturers can ensure precise and efficient handling of components, improving production efficiency and product quality.
Conclusion
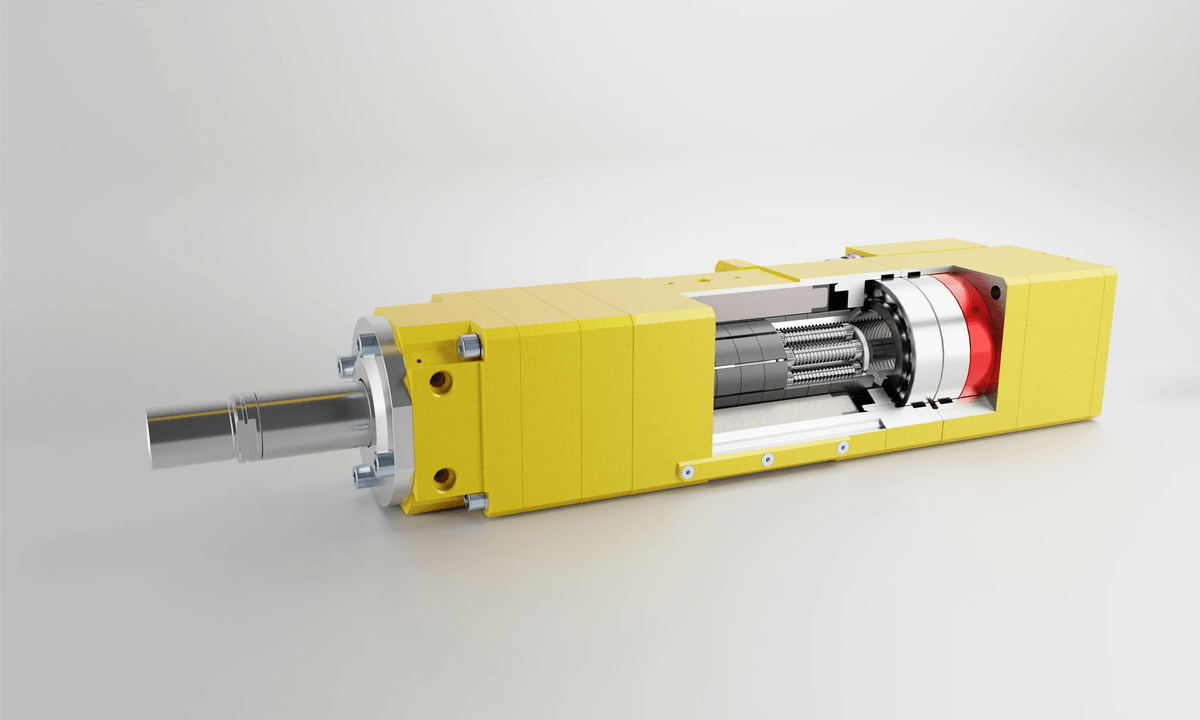
When implementing electrical actuators, it's crucial to consider your application's specific needs and choose the right type of actuator, whether an electric valve actuator, pneumatic actuator, or motorized actuator. The selection process should consider torque requirements, speed, and environmental conditions to ensure optimal performance.
Key considerations for actuator selection include evaluating the compatibility with existing systems, the precision required for valve control, and the ease of maintenance and operation. Working with reputable manufacturers like Haisen is important to ensure high-quality products that meet industry standards and provide reliable performance.
The impact of advanced actuators on industrial automation is significant, as these technologies continue to improve efficiency, safety, and productivity in various industrial sectors. With advancements in control systems and sensor technology, electric actuators are becoming increasingly integrated into smart automation solutions for enhanced performance and reliability.
With the growing demand for more flexible and adaptable industrial automation solutions, electric actuators are crucial in meeting these requirements. Their ability to provide precise and repeatable motion control, compact size, and low maintenance needs make them an ideal choice for modern manufacturing processes. As industries continue to embrace the concept of Industry 4.0, electric actuators will undoubtedly play a key role in driving the next wave of innovation and efficiency in industrial automation.